
Introduction
Chemical safety is a critical component of occupational health and safety, impacting millions of workers worldwide. The use of chemicals spans numerous industries, from manufacturing to healthcare, each presenting unique hazards that must be managed effectively.The Material Safety Data Sheet (MSDS) is an absolutely essential instrument in this endeavor.This document is essential for communicating the risks associated with chemical substances and providing guidance on safe handling practices. In this comprehensive guide, we will explore the intricacies of MSDS, its importance in chemical safety, and how it serves to protect workers and the environment.
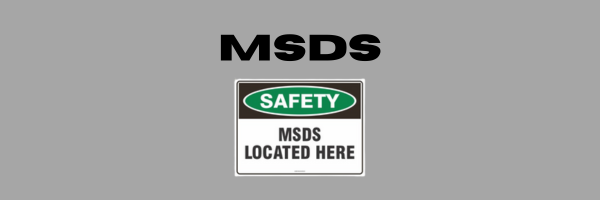
What is a (MSDS) Material Safety Data Sheet?
A Material Safety Data Sheet (MSDS), now often referred to as a Safety Data Sheet (SDS), is a detailed informational document prepared by the manufacturer or importer of a chemical. It describes the physical and chemical properties of the product, along with potential hazards, safe handling procedures, emergency control measures, and safety precautions. The primary purpose of an MSDS is to ensure that users of chemicals have the information they need to protect themselves and the environment from harm.
Regulatory Background
The development and use of MSDS are mandated by regulatory agencies worldwide. In the United States, the Occupational Safety and Health Administration (OSHA) enforces the Hazard Communication Standard (HCS), which requires that chemical manufacturers and importers provide MSDS for hazardous chemicals. Globally Harmonised System of Classification and Labelling of Chemicals (GHS), adopted by many countries, standardizes the classification and communication of chemical hazards, influencing the format and content of MSDS globally.
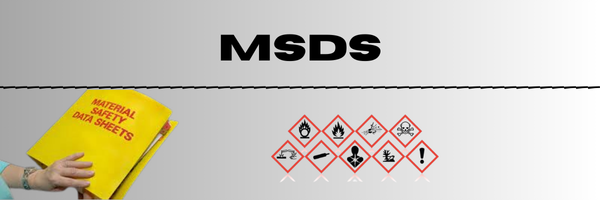
Components of an MSDS
An MSDS is typically structured into 16 standardized sections, each providing specific information about the chemical. Understanding these sections is crucial for effectively using and interpreting the information provided.
Identification of the Substance or Mixture
- Product identifier used on the label.
- Manufacturer or supplier details, including name, address, and phone number.
- Recommended use of the chemical and any restrictions on its use.
Hazard Identification
- Classification of the substance or mixture and its hazards.
- Name components include danger pictograms, signal words, hazard phrases, and preventative advice.
- Description of any hazards not otherwise classified.
Composition/Information on Ingredients
- Chemical identity and common names of the ingredients.
- Concentration or concentration ranges of all ingredients classified as health hazards.
- Chemical Abstracts Service (CAS) numbers and other unique identifiers.
First-Aid Measures
- Necessary first-aid instructions for different exposure routes (inhalation, skin, eye contact, ingestion).
- List of the most significant delayed as well as acute symptoms and consequences.
- Advice about urgent medical care and required specific therapy.
Fire-Fighting Measures
- Appropriate (as well as inappropriate) eliminating materials
- Particular dangers resulting from the chemical during a fire.
- specific protective equipment and firemen’s safeguards.
Unintentional Release Method
- Personal safety measures, equipment, and emergency protocols.
- Techniques and tools for confinement and spill or release cleanup.
- environmental safeguards against pollution.
Managing and Storing
- Precautions for safe handling, including protective measures and advice on general hygiene.
- Conditions for safe storage covering any incompatibilities.
Personal Protection and Control of Exposure
- Occupational exposure limits.
- Engineering controls and administrative measures to reduce exposure.
- Personal protective equipment (PPE) required, including respirators, gloves, and eye protection.
Physical and Chemical Properties
- Information on the substance’s appearance, odor, and physical state.
- Data on melting point, boiling point, flash point, solubility, and other relevant physical and chemical properties.
Stability and Reactivity
- Information on the chemical’s stability and the potential for hazardous reactions.
- Conditions to avoid, such as heat, sparks, or incompatible materials.
- Incompatible materials and hazardous decomposition products.
Toxicological Information
- Description of the toxicological effects of the chemical, including acute and chronic effects.
- Information on routes of exposure (inhalation, skin, eye contact, ingestion) and symptoms of exposure.
- Data on carcinogenicity, reproductive toxicity, and other specific health hazards.
Ecological Information
- Information on the environmental impact of the chemical.
- Information on ecotoxicity, persistence and degradability, bioaccumulative potential, and mobility in soil.Disposal Considerations
- Recommendations for safe disposal practices, including disposal of the chemical and its container.
- Information on local, regional, and national regulations governing disposal.
Transport Information
- UN number and proper shipping name.
- Transport hazard class and packing group.
- Special precautions for transport.
Regulatory Details
- Safety, health, and regulations regarding the environment particular to the chemical.
- Information on regulatory compliance and chemical safety assessments.
Additional data
- Date of the latest revision.
- Additional information, disclaimers, and references used in preparing the MSDS.
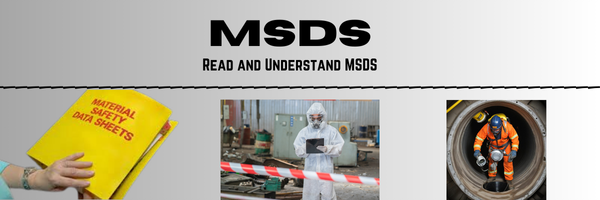
How to Read and Understand an MSDS
Understanding how to read and interpret an MSDS is vital for ensuring safety in environments where chemicals are used. Here are some practical tips:
Familiarize Yourself with the Format: MSDS documents follow a standardized format, making it easier to locate specific information. Take the time to become familiar with the layout and key sections.
Pay Attention to Hazard Identification: This section provides critical information about the potential risks associated with the chemical. Look for hazard symbols, signal words, and hazard statements to understand the severity of the hazards.
Focus on First-Aid Measures: Knowing the appropriate first-aid measures can prevent further harm in case of exposure. Familiarize yourself with the recommended actions for different types of exposure.
Understand PPE Recommendations: The exposure controls and personal protection section outlines the necessary protective equipment for handling the chemical. Ensure you have access to and understand how to use the recommended PPE.
Review Handling and Storage Instructions: Proper handling and storage of chemicals are essential for preventing accidents. Pay close attention to the conditions specified in the handling and storage section.
Consult Regulatory Information: This section provides insights into the legal requirements and guidelines related to the chemical. This can help ensure compliance with relevant regulations.
The Role of MSDS in Chemical Safety
Ensuring Workplace Safety
MSDS plays a vital role in promoting workplace safety by providing comprehensive information about chemical hazards and safety measures. By understanding and following the guidelines outlined in an MSDS, workers can minimize the risk of accidents, injuries, and health issues related to chemical exposure.
Legal and Compliance Aspects
Compliance with MSDS requirements is not just a best practice; it is often a legal obligation. Regulatory bodies such as OSHA in the United States and equivalent organizations worldwide mandate the availability and use of MSDS to ensure chemical safety. Failure to comply with these regulations can result in penalties, fines, and increased liability.
Case Studies and Examples
Real-life Scenarios and Lessons Learned
Chemical Spill Incident in a Manufacturing Plant
In a manufacturing plant, a worker accidentally spilled a container of a hazardous chemical. Fortunately, the plant had readily accessible MSDS for all chemicals on site. The workers quickly referred to the MSDS, which provided detailed information on the necessary first-aid measures, spill containment procedures, and personal protective equipment. The swift and informed response prevented serious injuries and environmental contamination.
Laboratory Safety Improvement
A research laboratory experienced a series of minor chemical exposure incidents due to improper handling and storage practices. After conducting a safety audit, the lab management implemented a comprehensive training program based on the MSDS for each chemical. This included regular drills and clear labeling of chemical storage areas. As a result, the frequency of incidents significantly decreased, and overall safety awareness improved.
Case Studies and Examples
- Regular Training and Education: Conduct regular training sessions to ensure that all employees understand how to read and use MSDS effectively.
- Accessibility: Make MSDS readily accessible to all employees, either in physical form or through digital databases.
- Emergency Preparedness: Incorporate MSDS information into emergency response plans and conduct drills to reinforce preparedness.
- Continuous Review and Update: Regularly review and update MSDS to ensure they reflect the latest safety information and regulatory requirements.
Technological Advancements and MSDS
Digital MSDS and Online Databases
With advancements in technology, digital MSDS and online databases have become increasingly popular. These platforms offer several advantages:
- Ease of Access: Digital MSDS can be accessed from any device with internet connectivity, making it convenient for workers to retrieve information quickly.
- Real-Time Updates: Online databases ensure that the most up-to-date information is available, reducing the risk of using outdated safety data.
- Searchability: Digital platforms allow for easy searching and filtering of MSDS, saving time and effort.
Future Trends in Chemical Safety Documentation
The future of chemical safety documentation is likely to see further integration of technology, including:
- Mobile Applications: Development of mobile apps that provide instant access to MSDS and other safety information, enhancing on-the-go safety management.
- Integration with Safety Management Systems: Linking MSDS databases with broader safety management systems for streamlined compliance and reporting.
- Interactive and Multimedia Formats: Utilizing interactive elements and multimedia to enhance the comprehension and engagement of safety information.
Challenges and Solutions in Managing MSDS
Common Issues Faced by Industries
- Keeping MSDS Up-to-Date: Ensuring that all MSDS are current and reflect the latest safety information can be challenging, especially in large organizations with numerous chemicals.
- Employee Training and Awareness: Maintaining a high level of employee training and awareness about MSDS can be difficult, particularly with high turnover rates.
- Compliance with Diverse Regulations: Navigating the complex landscape of national and international regulations related to MSDS can be daunting for companies operating in multiple regions.
Effective Management Strategies
- Centralized Management System: Implement a centralized system for managing and updating MSDS, ensuring consistency and accessibility across the organization.
- Regular Training Programs: Establish ongoing training programs to keep employees informed about the importance of MSDS and how to use them effectively.
- Regulatory Compliance Audits: Conduct regular audits to ensure compliance with all relevant regulations and to identify areas for improvement.
In conclusion
A basic part of chemical safety, Material Safety Data Sheets provide vital information to guard workers and the surroundings.
By understanding the purpose and contents of an MSDS, and implementing best practices in their management and use, organizations can significantly enhance their chemical safety protocols. As technology continues to evolve, the future of MSDS promises to offer even greater accessibility and effectiveness, ensuring safer workplaces for all.
In summary, the importance of MSDS in chemical safety cannot be overstated. They are not just regulatory requirements but vital tools for safeguarding health, safety, and the environment. By embracing a proactive approach to chemical safety and leveraging the advancements in digital documentation, organizations can navigate the challenges and achieve a higher standard of safety and compliance.
FAQs about Material Safety Data Sheets (MSDS) and Chemical Safety
An MSDS is a detailed document that provides information on the properties, hazards, handling, storage, and emergency procedures related to a specific chemical. It is essential for ensuring safe use and compliance with regulatory requirements.
MSDS are very essential for giving employees knowledge on how to properly manage and react to chemical risks, therefore avoiding mishaps and guaranteeing occupational safety.
Chemical manufacturers and importers are responsible for creating and providing an MSDS for each hazardous chemical they produce or import.
MSDS should be reviewed and updated whenever new information about the chemical’s hazards or safe handling procedures becomes available. Regular reviews, typically every three to five years, are also recommended.
An MSDS includes information on the chemical’s identity, hazards, composition, first-aid measures, fire-fighting measures, accidental release measures, handling and storage, exposure controls, physical and chemical properties, stability and reactivity, toxicological information, ecological information, disposal considerations, transport information, regulatory information, and other relevant details.
MSDS should be readily accessible to all employees, either in printed form or through an online database provided by the employer.
If an MSDS is not available, contact the manufacturer or supplier to request one. Employers are required by law to ensure that MSDS are available for all hazardous chemicals in the workplace.
The key sections of an MSDS includeIdentification; hazard identification; composition and information on ingredients; first-aid; fire-fighting; accidental release; handling and storage; Physical and chemical properties; exposure controls and personal protection; stability and reactivity; Toxicological data, ecological data, disposal issues, transportation information, regulatory data, and Other Information.
MSDS provide critical information on first-aid measures, fire-fighting procedures, and spill response, enabling workers and emergency responders to take appropriate actions during an emergency.
MSDS and SDS are essentially the same, with SDS (Safety Data Sheet) being the updated term used under the Globally Harmonized System (GHS) of Classification and Labeling of Chemicals. SDS follow a standardized 16-section format.
MSDS are generally required for hazardous chemicals. However, some employers may choose to provide MSDS for non-hazardous chemicals as well, for consistency and comprehensive safety information.
Yes, electronic MSDS are allowed as long as they are readily accessible to employees in their work area during their work shift.
The GHS is an international standard for the classification and labeling of chemicals. It aims to ensure consistent and clear communication of chemical hazards through standardized labels and Safety Data Sheets (SDS).
GHS standardizes the format and content of MSDS (now called SDS) to ensure consistent communication of chemical hazards worldwide. This includes standardized hazard classifications and labeling.
Hazard pictograms are standardized symbols used on MSDS and chemical labels to quickly convey the type and severity of hazards associated with a chemical.
Follow the first-aid measures outlined in the MSDS for the specific chemical. Seek medical attention if necessary, and report the exposure to your supervisor.
Employers should provide training on how to read and interpret MSDS. If you have questions, consult with your supervisor or a safety professional.
The Occupational Safety and Health Administration (OSHA) enforces regulations that require employers to provide MSDS for hazardous chemicals in the workplace and ensure they are accessible to employees.
First-aid measures in an MSDS typically cover actions to take in case of inhalation, skin contact, eye contact, and ingestion of the chemical.
MSDS provide guidance on spill containment and clean-up procedures, personal protective equipment (PPE) required, and environmental precautions to prevent contamination.
The PPE section of an MSDS outlines the necessary protective gear, such as gloves, goggles, respirators, and clothing, to safely handle the chemical.
Fire-fighting measures in an MSDS include suitable extinguishing media, specific hazards from the chemical during a fire, and special protective equipment for firefighters.
The handling and storage section of an MSDS provides guidelines on safe storage conditions, including temperature, humidity, and compatibility with other substances.
Disposal considerations in an MSDS offer recommendations for safely disposing of the chemical and its container, in compliance with local, regional, and national regulations.
Yes, MSDS are essential for compliance with occupational safety and health regulations, as well as environmental and transportation regulations related to hazardous chemicals.
If an MSDS indicates a chemical is carcinogenic, take additional precautions to minimize exposure, follow recommended handling and PPE guidelines, and implement engineering controls to reduce risk.
The ecological information section of an MSDS provides data on the environmental impact of the chemical, including its ecotoxicity, persistence, bioaccumulative potential, and mobility in soil.
MSDS are a vital resource for training programs, providing the necessary information to educate workers about chemical hazards, safe handling practices, and emergency procedures.
The physical and chemical properties section provides data on the chemical’s characteristics, such as appearance, odor, boiling point, and solubility, which are important for safe handling and use.
This section details the chemical’s stability under normal conditions, potential hazardous reactions, conditions to avoid, and incompatible materials.
The toxicological information section describes the health effects of the chemical, including acute and chronic effects, routes of exposure, and symptoms, helping workers understand the risks and take appropriate precautions.
Limitations of an MSDS include variability in the quality and completeness of information provided by different manufacturers, and the need for interpretation by trained personnel.
MSDS can be integrated into a company’s safety program by including them in training sessions, making them easily accessible, and using them as a reference for developing safety procedures and emergency response plans.
MSDS provide information on the environmental hazards of chemicals, guiding safe disposal practices and spill response to minimize environmental impact.
A chemical inventory should include a list of all chemicals in the workplace, along with corresponding MSDS, storage locations, and usage details to ensure proper management and safety.
MSDS are used in risk assessments to evaluate the hazards of chemicals, determine necessary control measures, and develop safety procedures to mitigate risks.
The transport information section provides details on the safe transportation of the chemical, including proper shipping names, hazard classes, and packing groups, ensuring compliance with transportation regulations.
Yes, MSDS are essential in research laboratories to ensure the safe handling, storage, and disposal of chemicals, as well as to inform emergency response procedures.
Employers can ensure employees understand MSDS by providing regular training sessions, accessible resources, and clear instructions on how to use and interpret the information.
The future of MSDS in chemical safety includes further integration with digital platforms, mobile applications, and advanced safety management systems, enhancing accessibility, real-time updates, and interactive features to improve chemical safety communication and compliance.

FAQs for Safety Supervisors on Responsibilities Related to Material Safety Data Sheets (MSDS) and Chemical Safety
Safety supervisors are responsible for ensuring that all MSDS are up-to-date and readily accessible to employees. They must also ensure that employees are trained on how to read and use MSDS, understand the hazards associated with chemicals, and know the appropriate safety measures and emergency procedures.
MSDS should be stored in a central, accessible location, such as a dedicated binder or an electronic database. Safety supervisors should make sure that all employees know where to find the MSDS and can access them easily during their work shifts.
The safety supervisor should obtain the MSDS for the new chemical, review it for potential hazards, and ensure it is added to the central MSDS repository. They should also update the chemical inventory and provide training to employees on the safe handling, storage, and emergency procedures for the new chemical.
Safety supervisors should establish a regular review schedule, typically annually, to ensure that all MSDS are current. They should also stay in contact with chemical manufacturers and suppliers for any updates or new information related to the chemicals used in the workplace.
Safety supervisors are responsible for developing and conducting training programs that educate employees on the importance of MSDS, how to read and interpret them, and how to apply the information to their daily tasks. This training should be part of the initial onboarding process and ongoing safety education.
Safety supervisors can verify understanding through regular quizzes, practical drills, and hands-on training sessions. They should also encourage employees to ask questions and provide feedback on the training material.
The safety supervisor should immediately contact the chemical manufacturer or supplier to request the missing MSDS. In the meantime, they should ensure that employees are aware of the absence and implement interim safety measures based on the known properties of the chemical.
Safety supervisors should include MSDS information in emergency response plans and conduct regular drills to ensure that employees know how to use the MSDS in case of an emergency. This includes knowing the location of the MSDS and understanding the procedures for dealing with spills, exposures, and fires.
During a chemical spill, the safety supervisor should first ensure the safety of all personnel by evacuating the area if necessary. They should then consult the MSDS for the spilled chemical to determine the appropriate containment and cleanup procedures and ensure that all responders are using the recommended personal protective equipment (PPE).
Safety supervisors should regularly review OSHA regulations and guidelines related to MSDS and chemical safety. They should conduct periodic audits to ensure compliance, update procedures as needed, and maintain accurate records of all MSDS and employee training.
Safety supervisors are key to hazard communication, ensuring that all chemical hazards are clearly communicated to employees through labels, signs, training, and access to MSDS. They must ensure that the workplace complies with the Hazard Communication Standard (HCS) set by OSHA.
In the event of a chemical exposure, the safety supervisor should follow the first-aid measures outlined in the MSDS and seek immediate medical attention if necessary. They should also document the incident, conduct an investigation to determine the cause, and implement corrective actions to prevent future occurrences.
The hazard identification section provides critical information about the potential risks of a chemical, including health, physical, and environmental hazards. Safety supervisors must use this information to assess risks, implement control measures, and communicate hazards to employees.
Safety supervisors should review the handling and storage section of each MSDS and ensure that chemicals are stored under the recommended conditions. This includes maintaining appropriate temperature, humidity, and segregation from incompatible substances.
The safety supervisor should provide additional training and clarification to the employee, ensuring they fully understand the MSDS information. This may involve one-on-one sessions, practical demonstrations, or supplementary materials.
The toxicological information section helps safety supervisors understand the health effects of exposure to a chemical. They can use this information to implement appropriate PPE, engineering controls, and administrative measures to minimize exposure and protect workers’ health.
Safety supervisors must ensure that the environmental precautions and disposal considerations outlined in the MSDS are followed. This includes proper disposal of chemicals and containers, spill prevention measures, and compliance with environmental regulations.
The stability and reactivity section of an MSDS provides information on the chemical’s reactivity hazards. Safety supervisors should use this information to avoid conditions that could cause dangerous reactions and ensure safe storage and handling practices.
If a safety supervisor identifies an outdated or inaccurate MSDS, they should contact the chemical manufacturer or supplier to obtain the correct information. They should also update the central repository and inform employees of the changes.
Safety supervisors can contribute to continuous improvement by regularly reviewing and updating safety procedures, conducting risk assessments, seeking employee feedback, and staying informed about new safety regulations and best practices.
The physical and chemical properties section provides data on characteristics such as melting point, boiling point, and solubility. Safety supervisors use this information to understand how the chemical behaves under different conditions and to develop appropriate safety measures.
A successful MSDS training program should include clear explanations of MSDS sections, hands-on demonstrations, practical exercises, regular refresher courses, and assessments to verify understanding. Training should be tailored to the specific needs and tasks of the employees.
The ecological information section helps safety supervisors understand the environmental impact of a chemical. This information is used to develop spill response plans, waste disposal procedures, and environmental protection measures.
Best practices for conducting an MSDS audit include: creating a comprehensive inventory of chemicals, verifying that all MSDS are up-to-date, checking accessibility for employees, reviewing training records, and ensuring compliance with regulatory requirements.
Safety supervisors can encourage engagement by involving employees in safety meetings, soliciting feedback, recognizing safe practices, providing incentives for compliance, and fostering a culture of safety through open communication and leadership.
If a supplier does not provide an MSDS, safety supervisors should request it in writing and document the request. If the supplier fails to comply, the supervisor should consider sourcing the chemical from a different supplier who meets regulatory requirements.
The transport information section helps safety supervisors ensure that chemicals are transported safely and in compliance with regulations. This includes proper labeling, packaging, and documentation for shipping.
Safety supervisors play a crucial role in hazard communication by ensuring that all chemical hazards are clearly labeled, that MSDS are accessible, and that employees are trained on recognizing and responding to chemical hazards.
Safety supervisors can address language barriers by providing MSDS and training materials in multiple languages, using visual aids and symbols, and ensuring that interpreters or bilingual trainers are available if needed.
During a chemical exposure incident, the safety supervisor should follow the first-aid measures outlined in the MSDS, ensure the affected employee receives medical attention, document the incident, and investigate the cause to prevent future occurrences.
Safety supervisors should stay informed about international MSDS regulations, such as those under the Globally Harmonized System (GHS), and ensure that their practices and documentation comply with these standards.
The first-aid measures section provides critical information on how to respond to chemical exposure incidents. Safety supervisors use this information to train employees and develop emergency response plans.
For chemicals with unknown properties, safety supervisors should implement conservative safety measures, seek additional information from the manufacturer or supplier, and ensure that employees are aware of the potential risks and precautions.
Common challenges include keeping MSDS up-to-date, ensuring accessibility, training employees, maintaining compliance with diverse regulations, and managing a large volume of MSDS for multiple chemicals.
Safety supervisors can use digital tools and software for MSDS management, which offer features like electronic access, real-time updates, search functionalities, and integration with other safety management systems.
Safety supervisors lead incident investigations to determine the cause of chemical-related incidents, using MSDS information to identify contributing factors and implement corrective actions to prevent recurrence.
Safety supervisors should verify that the hazard classifications in MSDS align with regulatory standards and guidelines, and work with manufacturers and suppliers to correct any discrepancies.
If an MSDS is suspected to be incomplete or inaccurate, safety supervisors should contact the manufacturer or supplier for clarification and ensure that the correct information is obtained and disseminated to employees.
Promoting a culture of safety involves regular communication, ongoing training, leading by example, recognizing safe behaviors, encouraging reporting of safety concerns, and continuously improving safety practices based on feedback and incident reviews.
Pingback: Heat Stress and Stroke: Prevention Tips for Safety Supervisors -